The demand for oligonucleotide-based drugs is constantly increasing. To meet the increased demand, pump and system manufacturer LEWA is supplying pharmaceutical supplier Bachem with a new inline dilution system to expand production capacities at the company’s main site in Bubendorf (Switzerland) in the company’s largest production building to date. The system enables precise and flexible dosing of dilution solutions.
In the production of fine chemicals for biopharmaceuticals and active pharmaceutical ingredients, purification in the downstream processing of substances through chromatography and filtration processes is of crucial importance. For this purpose, the preparation of buffer solutions with high mixing ratio accuracy is critical, and the respective formulation of the individual solutions must be highly variable. As active pharmaceutical ingredients (APIs) experience increasing global demand, these process steps must be increasingly automated and integrated into complete production lines. This way, solutions can be mixed directly at the point of use according to the need for specific dilutions from available concentrates, which accelerates the entire manufacturing process while also reducing space requirements. “One of the biggest challenges with inline dilution is maintaining consistently reproducible quality of the buffers required in each case,” says Pietro Pettoruto, Managing Director of LEWA Switzerland AG. One requirement for this is precise control of the flow rates and the resulting dilution ratios. The pumps used must be hygienic, robust and designed for continuous operation. In order to benefit from detailed knowledge and experience in high-precision metering and mixing, Bachem commissioned LEWA to provide a corresponding system for the new production building in Bubendorf. Bachem has been working with LEWA for many years—LEWA has already equipped other locations with hygienic metering pumps.
“The innovative system concept is a customized inline dilution system designed as a package unit (PU) for the downstream process in complex oligonucleotide production,” adds Roland Schwab, who is responsible for systems in the Sales Process Industry & Downstream department at LEWA. The system has five process inlets and outlets as well as four drains to ensure flexible and continuous media transport. Due to special customer requirements, the system is designed for use in Ex zone 2. The inline dilution system provides high-accuracy buffer solutions for a semi-continuous chromatography system.
Patented diaphragm metering pumps ensure high production reliability
“Since very different flow rates are required in the production of the dilution solutions, Bachem stipulated in its specification (URS) that flow rates of a minimum of 40 l/h and a maximum of 2,500 l/h must be possible,” says Pettoruto. In order to be able to cover this large adjustment range flexibly, a total of five LEWA ecodos hygienic pumps are integrated into the plant, driven by mechanically actuated multilayered sandwich safety diaphragms. As a result, the risk of contamination, such as with hydraulic oil, is avoided. Due to the GMP environment, hygienic designs with certified construction materials (FDA, USP) were selected, with all wetted metallic parts electropolished and having a surface roughness of Ra ≤ 0.5 µm. Thanks to the hygienic design, which avoids dead spaces almost entirely, the pumps are very easy to clean in a CIP (cleaning in place) process without prior disassembly. In addition, stainless steel 1.4435 with low delta ferrite content and highly corrosion-resistant stainless steel 1.4529 (equivalent to AL-6XN) were used as materials. This makes the pumps suitable for pumping highly corrosive and flammable fluids in oligonucleotide production over the long term. The patented four-layer PTFE sandwich diaphragm also plays a major role in this. It is extremely stable and ensures that continued operation is possible even in the event of a diaphragm rupture, thus providing a high level of process safety. Built-in diaphragm rupture signaling immediately reports a corresponding malfunction during operation without contaminating the rest of the process line. This ensures a level of production safety that is unparalleled in the pump sector.
The preparation of buffer solutions in the chromatographic environment requires precise adherence to flow rates of the individual pump lines. The flow rates are determined with highly accurate mass-flow meters and set precisely to the specified target values via the speed control of the metering pumps. To control the process conditions, the pH value and conductivity are also monitored online.
LEWA as a reliable expansion partner
The inline dilution system described is not the first project LEWA has implemented for the leading supplier to the global Pharma and Biotech industry. “We have been partners with Bachem for several years and have supplied different pumps according to specific customer requirements,” says Pettoruto. For example, chromatography systems at the other locations already operate with the same proven technology: LEWA ecodos pumps in the hygienic design. For applications in the traditional pharmaceutical sector with higher pressure levels, LEWA ecoflow models were used.
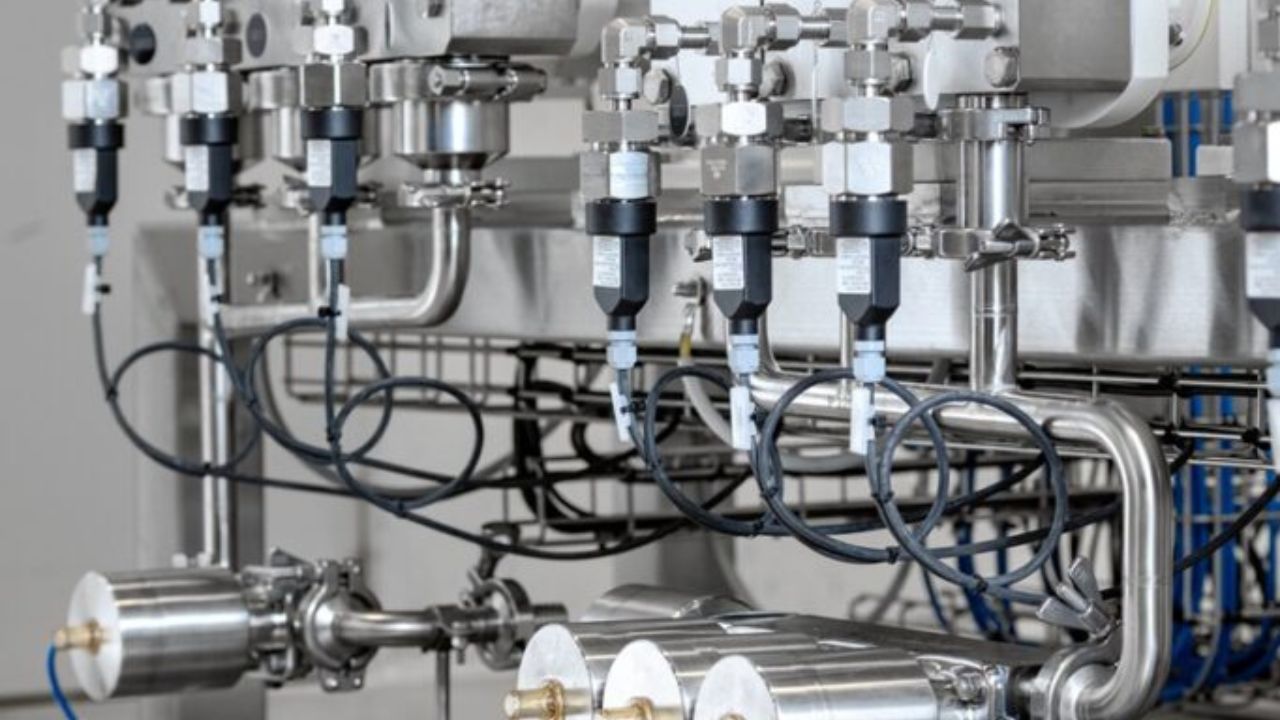
Oligonucleotide Production: Dilution System for Production with Highly Varying Flow Rates
Prev Post
NETZSCH Pumps USA Highlights Complex
Next Post
Strengthening the Market Position in