Wastewater from ethylene production in chemical and petrochemical industries as well as in petroleum refineries poses a particular challenge in terms of water treatment. As it contains hazardous pollutants such as sulfides and mercaptans, that do not respond to traditional treatment methods, chemical companies and refineries resort to Wet Air Oxidation (WAO).
With elevated temperature and high pressure, this method is able to achieve oxidation of the critical compounds, making the liquid suitable for subsequent biological treatment. The Best Available Technique (B.A.T.), as acknowledged by the European Union IPPC Commission, is the TOP – Wet Air Oxidation process developed by the Italy-based process equipment provider 3V Group. Based on this technology, 3V Tech manufactures industrial scale modular systems that reduce the chemical oxygen demand (COD) of spent caustic up to 99%, with the residual COD being detoxified, decolored and almost entirely biodegradable. To handle the spent caustic water, however, the process requires hermetically tight, high pressure pump technology that is suitable for dangerous fluids and allows for adjustable flow rates as well as high positioning accuracy. For their TOP plants, 3V Tech therefore relies on LEWA diaphragm pumps, whose patented PTFE diaphragm heads provide highest chemical resistance.
“When it comes to industrial wastewater from petrochemical and chemical plants, the effluent is contaminated with heavy and complex organic molecules. These are particularly difficult to deal with,” explains Camilla Navicello, Sales Expert from LEWA Italy Srl. “Spent caustic liquors are not just odorous and highly colored, but, more importantly, contain sodium sulfides, mercaptans, phenols and emulsified hydrocarbons. Wet Air Oxidation (WAO) is used to degrade the complex organic loaded caustic water at high pressures and temperatures with the addition of oxygen in an efficient, environmentally friendly and flexible way.” Through this process, most hazardous pollutants can be degraded into easier treatable substances such as carbon dioxide, water vapor, sulfite and sulfate, and simpler organic forms, which are biodegradable in a second conventional process stage.
Among the world market leaders in terms of WAO ranks the Italy-based 3V Group with the TOP – Wet Air Oxidation process. In a process similar to flameless burning, this method is able to oxidize heavy and complex molecules at high temperature and pressure levels, reducing the COD of the hazardous liquid up to 99% and permanently removing any odor and color. Subsidiary company and process equipment provider 3V Tech realizes this method on an industrial scale, manufacturing turn-key modular systems specifically for the toxic, non-biodegradable spent caustic.
Hermetically tight and safe pumps handling hazardous fluids
To withstand the heavily polluted and odorous water, TOP – Wet Air Oxidation plants must be equipped with a hermetically tight and safe pump. In that respect, 3V Tech approached LEWA Italy, as the pump specialists have extensive experience in this type of application. Drawing on the joint expertise of the teams from LEWA Germany and LEWA Italy, the latter thus recommended energy efficient LEWA ecoflow diaphragm pumps for this challenging project: “Our diaphragm pumps are characterized by the material as well as design of the patented sandwich diaphragm itself,” explains Navicello. “Firstly, it is made from PTFE, which has higher chemical resistance than conventionally used materials like EPDM. Secondly, the pump is continuously monitored by the reliable DPS diaphragm protection system.” The DPS instantly detects if one of the diaphragms is damaged, while the sandwich diaphragm design is keeping the entire pump head hermetically tight even after damage has occurred. This particular construction and the special diaphragm system are the key to providing the state-of-the-art pump characteristics required for efficient and safe WAO plants.
Regarding the material of the other wetted components of the LEWA ecoflow pumps, standard 316/316L high-grade steel is usually fine to prevent corrosion even with highly aggressive spent caustic containing sulfide. Depending on the specific fluid consistency and operating temperatures, however, it may be necessary to choose special alloys such as Ti-Alloy or Hastelloy, which provide even higher chemical resistance. Ex-proof designs are manufactured, depending on the safety zone requests on site. “All pump components are designed to reliably maintain their excellent suction and overall operating conditions for extended periods of time and require low maintenance,” adds Navicello. “The reliability, process safety and operator friendliness of theses pumps are outstanding. They are essential qualities when dealing with such toxic and odorous types of wastewater for very different locations worldwide.”
Modular pump design for various ethylene and refinery applications
Through their cooperation with 3V Tech and supplying LEWA diaphragm pumps for TOP – Wet Air Oxidation for spent caustic plants, LEWA Italy has gained extensive experience with different WAO applications. Depending on the amount of wastewater to be treated, LEWA pumps in different designs are used, with the very robust and compact LEWA triplex pump series being best suited for lager installations. Thanks to their variable modular design, LEWA can realize specific pump solutions for WAO applications to meet all kinds of requests. Some locations even require challenging documentation and pump tests, which are also provided by the pump manufacturer. “Although LEWA Italy is in charge of the 3V Tech project, we would like to thank our colleagues from Germany for their close cooperation. With LEWA’s international presence, we are capable of realizing these types of WAO solutions all over the world,” Navicello concludes
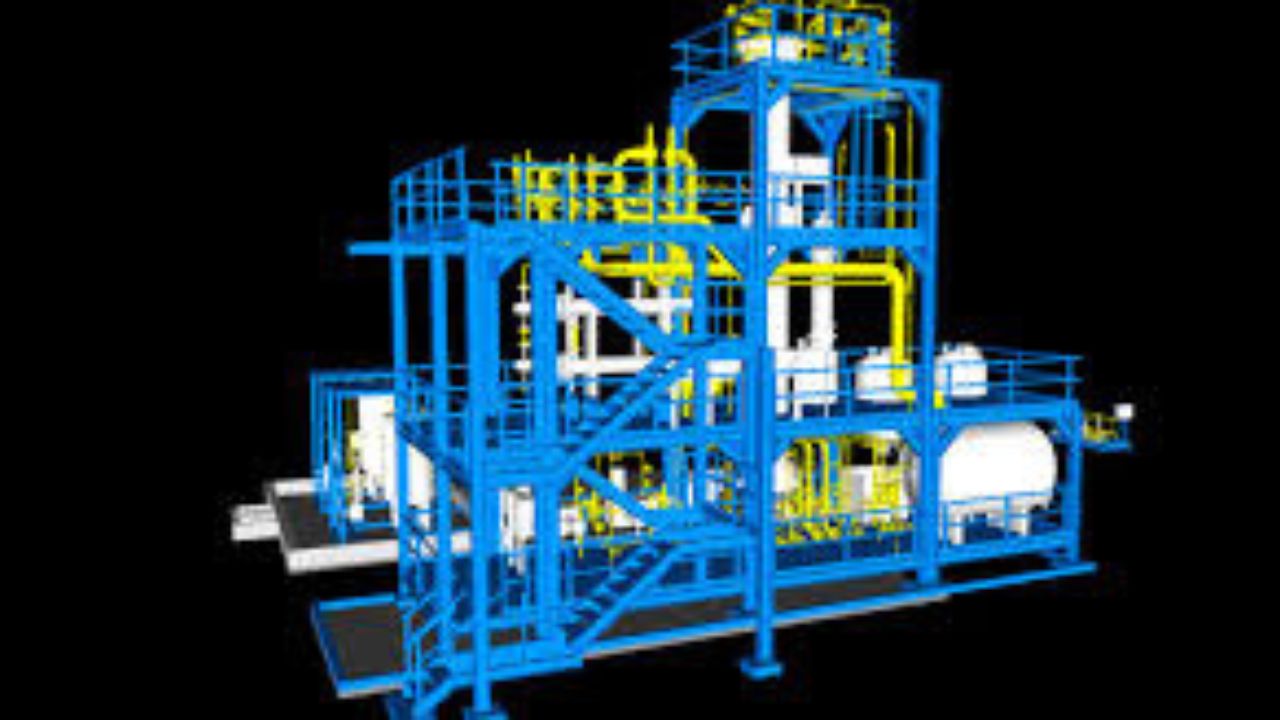
Wet Air Oxidation – Treating Spent Caustic Liquors
Prev Post
Messe Frankfurt Increases Its Presence
Next Post
Smith & Loveless Introduces a